Injection molds are the workhorses of the plastic molding world, and poor maintenance leads to inferior parts and lost production time. Fortunately, preventative maintenance is less expensive than repairs and replacements.
Proper maintenance includes periodic cleaning and lubrication of the mold. Other key techniques include conducting thorough mold trials before mass production to catch defects such as lack of material or bubbles, and making adjustments based on trial results. Contact Florida Plastic Mold Maintenance now!
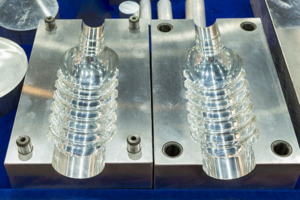
When it comes to cleaning plastic soap molds, it’s important to use gentle methods so you don’t damage the mold. Avoid harsh chemicals and abrasive sponges that can cause scratches and nicks in the surface. Instead, opt for warm water and a soft brush or paddle to scrape off the soap residue.
After washing the soap molds, make sure to dry them thoroughly. A high-quality lint-free cloth will do the trick, or you can use an air dryer if you have one available. Be sure to also wear gloves and a mask while cleaning to avoid inhaling fungal spores.
Once the soap molds are clean, apply a silicone release agent to keep them in good condition. This prevents a build-up of contaminants on the mold surface that can lead to defects in finished parts.
Injection molds are an essential tool in the plastic manufacturing industry, facilitating the production of complex components. However, improper maintenance can result in mold breakdowns and decreased productivity. A preventative maintenance program for injection molds includes regular cleaning, inspection, and lubrication.
Cleaning plastic molds is an important part of preventative maintenance, as it removes any residual materials from the surfaces of the parts. A clean mold surface promotes a more accurate inspection process, and it can extend the lifespan of the mold.
A good cleaning and inspection regimen can help reduce downtime due to repairs and improve efficiency. Injection molds that are cleaned and inspected regularly will produce quality, consistent products. They will also last longer, reducing the need for replacements and saving manufacturers money. Injection molds should be cleaned after each run and inspected periodically for cracks, leaks, or other signs of damage.
Inspection
Routine inspections detect wear and tear before it affects the quality of a plastic part. Inspections identify problems that can be corrected to prevent a loss in production time and cost. Injection molds should be inspected before and after every run, and records of each maintenance activity should be kept. The frequency of inspections should depend on the number of cycles a plastic mold is expected to endure, but all molds need routine cleaning, lubrication, and a full inspection for damage.
The most important component of a regular inspection is to make sure the injection mold and its parts are clean. This involves wiping down the mold with a cleaner and then inspecting for debris and dirt. It’s also important to check that the injection mold is a good fit for its press, and that it has all the necessary fittings. Finally, it’s essential to make sure all components of the injection mold are functional, such as the ejector units and the runner system.
During general maintenance, an inspector examines all of the mold’s surfaces for defects such as flashing, sink marks, weld lines, and warpage. These can be caused by a variety of factors, including a non-uniform cooling rate and material shrinkage. An inspector should also look at the runners and sprues of the mold to see if they are free of obstructions, leaking oil, or rust.
Injection molds can last from hundreds to over a million cycles, depending on the environment, maintenance, molding conditions, and structure design. Performing the proper maintenance can extend the life of a plastic injection mold and help ensure high-quality products for the consumer. By keeping the injection mold clean, lubricating it regularly, and conducting frequent inspections to spot issues, companies can reduce repair costs and avoid production delays.
Lubrication
Using advanced maintenance techniques will reduce friction between mold components and help them last longer. Lubrication prevents parts from binding or sticking and helps to lessen the amount of stress placed on the mold overall. Injection molds are exposed to high temperatures and pressure, so using the right lubricant is key.
Lubrication also makes it easier to conduct inspections of the mold, as they will be more responsive and able to open and close more easily. This will improve quality and increase productivity and efficiency.
Regularly cleaning plastic injection molds prevents residue buildup that can affect the quality of molded parts. This includes removing adhered contamination, burned gases, and other contaminants. Conventional cleaners can be too aggressive or unsafe for use with food grade products. Using advanced maintenance methods, such as plasma treatment and diamond-like carbon coating (DLC), will remove contaminants more thoroughly without being harmful to the plastic or the environment.
Injection molds are costly investments. Like any mechanical equipment, they will experience wear and tear as they are used. Taking steps to protect the investment, including routine inspections, cleaning, and lubrication, will extend the life of the mold and ensure consistent production and quality for the life of the tool.
Injection molds that are subjected to harsh, dirty environments will have shorter lifespans than those in clean, controlled environments. In addition, the temperature settings of an injection molding machine can have a significant impact on a mold’s performance and longevity. It is important to calibrate and test the temperature setting of the molding machines regularly to ensure that they are operating within their designated range. Regularly inspecting and cleaning heating elements, thermocouples, and temperature sensors will also help to prolong the life of the molds.
Heat Treatment
Heat treatment is the process of heating and cooling metal to alter its properties. This can increase strength, reduce deformation and improve corrosion resistance. It is an important part of the manufacturing process for most metal products and is used in a wide variety of industries. Typical heat treatment processes include annealing, case hardening, precipitation strengthening and tempering.
The surface of plastic molds is often exposed to abrasion and chemical attack, so it needs to be treated. Chromium plating is an effective method of surface treatment. It has a high passivation ability and can withstand a wide range of acids. The coating is also very hard, making it resistant to scratching and abrasion. The chromium layer does not react with molten plastics, so it is safe to use for injection molding.
Another common heat treatment is nitriding. This is a thermochemical process that creates a dense, wear-resistant layer of titanium nitride. This layer is ten times harder than carbon steel and is highly corrosion-resistant. It is used on dies, tools and machine parts in abrasive environments, such as plastic molding. Its low processing temperature and lack of mold distortion make nitriding ideal for low-volume production.
In addition to improving the strength and wear resistance of the workpiece, heat treatment also enhances its impact toughness and internal stress distribution. This is particularly important for complex molds with high alloy content. Proper preliminary heat treatment can eliminate meshed secondary cementite and chain carbides in high-carbon die steels and promote the formation of a more homogenous spheroidizing structure. Cryogenic treatments can also be used to further enhance the mechanical properties of dies and ensure long-term stability.
Replacement
Molds are a critical investment, and it’s important to ensure that they operate at peak performance. Regular maintenance can extend their lifespan, improve the quality of parts produced, and enhance productivity.
The conditions in which a plastic injection mold operates heavily affects its life expectancy. Cleaner environments lead to longer mold lives than dirty ones. Similarly, high-quality plastics have better longevity than low-quality materials.
Injection molds need regular cleaning to prevent the buildup of contaminants, which can lead to defects in molded products. This includes removing sprue debris, wiping the inside of the mold, and re-lubricating components like leader pins and bushings. Injection molds also need to be cleaned of water leaks around the static seals and where dissimilar metals come into contact.
Keeping up with maintenance and repairs helps to minimize downtime caused by production problems. When a problem is identified, it can be quickly and efficiently repaired. This can reduce rework costs and boost production efficiency.
Maintaining a consistent cycle time also makes it easier to meet production targets. If the cycle times of a plastic injection mold are erratic, it can be difficult to meet production goals and may result in costly rework. However, well-maintained injection molds can produce parts at consistent times, enabling companies to make just-in-time inventory decisions.
Finally, implementing a mold refurbishment schedule based on usage or number of shots can help operators determine when to repair, refurbish, upgrade, or replace a mold. This can be especially useful when a mold has reached the end of its useful life and requires replacement components. It’s important to keep in mind that a new mold can cost as much as 30 percent less than repairing and upgrading an existing one.